About Feather Microphones//
MICROPHONES
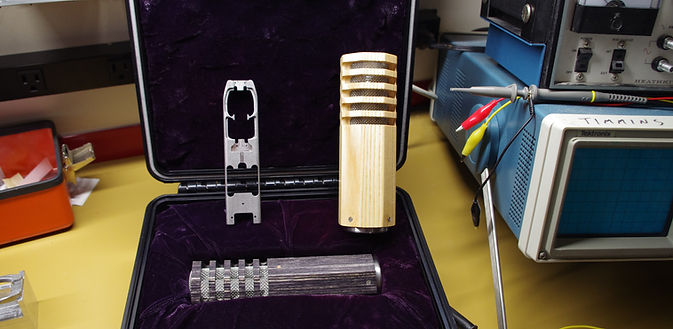
Everybody knows that microphones will color the sound that is being recorded; otherwise, we would all use $50 reference mics to record everything. Every mic colors sound, pick the color you want.
About 20 years ago, I was helping a friend at his studio. The lead singer would tap or thunk the mic (a very nice vintage condenser) every time he walked by. The ring that was produced each time he did it, was not only extremely irritating, but burned itself into my memory. I started hearing the resonance of the microphone bodies in nearly every raw track. While we can remove most of these artifacts in post-production, wouldn’t it be nice if we didn't have to. What about the musical information that we inadvertently remove when "tuning" a track to remove microphone artifacts?
While sharing a beer after the session, I told my friend, "I think microphones are being made wrong”. “Shouldn’t they be made more like musical instruments?"
Well, it had been 20 years and I hadn't seen anybody build a microphone as a musical instrument, as opposed to a scientific instrument entombed in a metal tube or box. At my 40th birthday party, I told everyone celebrating with me that I was going to build this microphone. For the next 6 months, I sold everything I could afford to lose to get the funds I would need to start prototyping the microphones. 4 axis CNC milling machine, shears, forming equipment, 3D printer, more audio test gear...I repurposed the garage and two rooms in the basement for manufacturing, testing and final assembly. It was nearly 2 years to the day that I received my "patent pending".
What is so great about this mic?
This microphone is not like any other on the planet. Rather than start the design by coppying other ribbon mics from the past or present, I started with the idea that a microphone should be built as a musical instrument, and applied the basic principals of ribbon mic operation and modeled the design with phisics.I went through innumerable variations before the final design became apparent. The end result is a ribbon mic supperior in it's accuracy, warmth, and frequency response.
There is not one single piece from China on these mics. It was designed from the ground up based on real world physics. I have removed the pole pieces allowing for the smallest path from the front of the mic to the back, allowing for high frequency extension without resonator plates that ruin transient response. Very strong custom neodymium magnets have been made for these microphones to produce the magnetic flux necessary. I have done everything possible to remove unnecessary items from the microphone that may get between your sound and the output of the mic.
The entire motor assembly slides into the wood or composite microphone body as a press fit. The motor becomes coupled to the body instead of being decoupled the way most mics are currently made. When coupled, any resonance not attenuated by the combination will have the tonal characteristics and timbre of the wood body, instead of the metallic ring of a metal body as other microphones are made. Pat Pending.
I am currently making Birch composite bodies, Ash bodies, and my favorite, Cocobolo bodies.
The composite bodies have the most internal dampening to them (very neutral), The Ash have good dampening qualities, but are a bit livelier. The Cocobolo have the least internal dampening, but are lively and sound incredible on horns, sopranos, or anything with rich uper harmonic content that can't be audibly observed with conventional ribbon mics.
I am currently expanding the wood selection to be available, but will take time since each piece of wood has to be carefully cured so that it will retain its dimensional stability over time and survive the manufacturing process. The curing and incremental machining process takes months, if not far longer. There have had certain pieces of wood curing for over a year, and they are still not ready to become a microphone.
When creating the microphone, I set a secondary challenge for myself. That challenge was a 100% made in the U.S. microphone. Outside of the Cocobolo wood, and Aluminum from Japan, I have succeeded. I even source the cases from S3, a US case manufacturer. The transformers are made for Feather Microphones by Cinemag. I feel it is important to keep our manufacturing alive and well in this country. While building ribbon mics alone won't make a huge drop in the bucket, you can feel proud knowing that your purchase will help people support families in Seattle, California; even Georgia.
You can read more about where each part of the microphone comes from by pressing the button below.